Create and send online quotations and invoices, track sales, monitor staff performance, and sell & sync all your products via our POS and more.
Author : Haya Assem
Reviewed By : Enerpize Team
How To Manage Auto Parts Inventory Efficiency
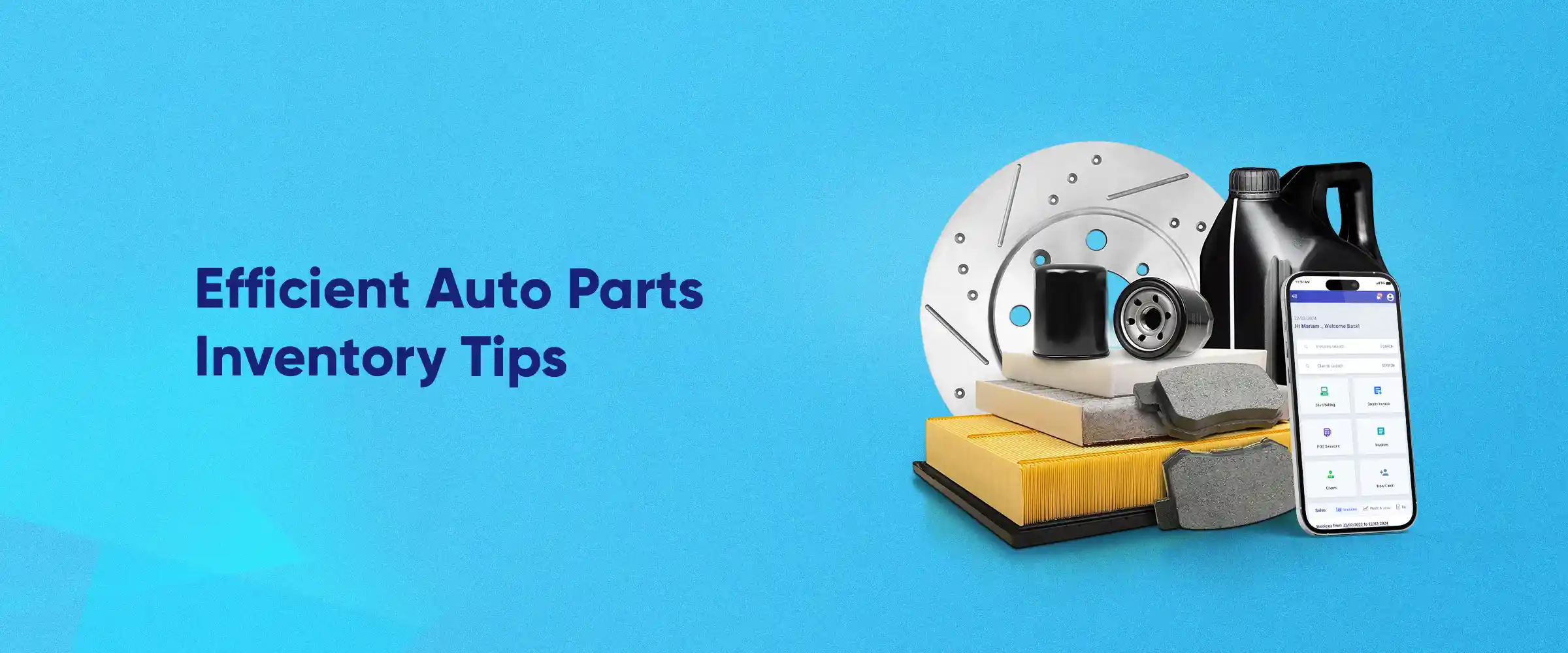
Efficient auto parts inventory management is essential for reducing costs, preventing stock shortages, and ensuring smooth operations in auto repair businesses. By leveraging smart inventory strategies, automation, and data-driven decision-making, businesses can enhance efficiency and improve customer service.
Key Takeaways
- Master Auto Parts Inventory Management – Effective inventory control reduces costs, prevents shortages, and enhances efficiency in auto repair businesses.
- Use the Best Auto Parts Inventory Software – Automate stock tracking, restocking, and reporting while integrating with sales and purchasing.
- Organize & Categorize Inventory – Learn how to organize parts inventory by sorting items by type, brand, and usage for quick access.
- Monitor Stock Levels – Set minimum and maximum thresholds and conduct cycle counts to maintain accurate inventory.
- Analyze Fast & Slow-Moving Parts – Stock high-demand items while using discounts or promotions to clear slow-moving inventory.
- Optimize Storage & Organization – Use labels, structured storage, and strategic placement for easy retrieval.
- Track Supplier Performance – Maintain relationships with multiple suppliers to ensure timely deliveries and consistent quality.
- Use Data & Analytics – Leverage sales trends and demand forecasting to optimize purchasing and stock levels.
Tips for Managing Auto Parts Inventory Efficiency
To smoothly maintain auto parts inventory operations, you need to implement an efficient inventory management system, track stock levels accurately, optimize storage organization, and ensure timely restocking. Proper categorization, supplier coordination, and data-driven forecasting also play a crucial role in preventing shortages and overstocking. By adopting these strategies, businesses can reduce costs, improve efficiency, and enhance customer satisfaction.
1- Implement an Inventory Management System
Use automated inventory management software to track stock levels in real time, minimizing errors and improving efficiency. Manual tracking can lead to misplaced parts, miscalculations, and delays, all of which can be avoided with the right system.
Ensure the software integrates seamlessly with sales, purchasing, and accounting systems. This ensures that when a sale is made or a new shipment arrives, inventory levels update automatically. Integration also helps in generating reports, tracking profitability, and forecasting future demand.
Read Also: 7 Benefits of Implementing Automotive Repair Software in Your Workshop
2- Categorize Inventory Properly
Organizing parts by type, brand, model compatibility, and usage frequency makes it easier for staff to find the right item quickly, reducing downtime in operations. A well-structured categorization system ensures efficiency and prevents duplication.
Use SKU codes, barcodes, or RFID tags to simplify tracking. Scanning a barcode is much faster and more accurate than manually entering part details. It also reduces the risk of human error, ensures smooth check-ins and checkouts, and streamlines the inventory audit process.
3- Monitor Stock Levels Regularly
Setting minimum and maximum stock thresholds ensures that critical parts are never out of stock while also preventing excess inventory that could lead to higher holding costs. When stock reaches a predefined level, automated reordering can be triggered to maintain a healthy balance.
Implement cycle counting, where specific sections of the inventory are checked periodically rather than waiting for a single annual count. This helps catch errors and discrepancies early, ensuring more accurate records and reducing the risk of missing parts when they are needed.
Read Also: What is a Perpetual Inventory System?
4- Utilize Just-In-Time (JIT) Inventory
JIT inventory management minimizes the need for excess storage by ordering parts only as needed, reducing waste and freeing up capital. However, this approach requires a reliable supply chain to ensure quick deliveries.
Build strong relationships with multiple trusted suppliers to ensure on-time deliveries. Having backup suppliers helps avoid disruptions in case of unexpected delays, price hikes, or supplier issues.
5- Track Fast-Moving & Slow-Moving Parts
Regularly analyze which parts sell quickly and which ones take up storage space. Keeping popular parts in stock ensures that customer demands are met without delays, while slow-moving items should be handled strategically.
To manage slow-moving inventory, offer discounts, promotions, or bundled deals to encourage sales. Excess stock can take up valuable space, so clearing it out through strategic pricing can improve cash flow and optimize storage utilization.
6- Optimize Storage & Organization
Use clear labeling and organized storage to make locating parts faster and reduce search time. Employees should be able to identify and retrieve any part they need without confusion quickly.
Store frequently used parts in the most accessible locations, such as near workstations or entry points, while lesser-used items can be placed in less accessible areas. A well-organized warehouse reduces retrieval time, minimizes mistakes, and improves overall workflow.
7- Monitor Supplier Performance
Track supplier reliability by monitoring delivery timelines, order accuracy, and product quality. Delays in receiving parts can slow down business operations, so consistent supplier performance is crucial.
Maintain relationships with multiple suppliers instead of relying on just one. This ensures that you have alternatives to prevent stock shortages or price fluctuations if a supplier fails to meet expectations. A diversified supply chain adds flexibility and resilience to inventory management.
Read Also: Why Do You Need Business Insurance For Your Auto Repair Shop?
8- Use Data & Analytics for Forecasting
Leverage data analytics to track sales trends, seasonal demand, and recurring customer needs. For example, some auto parts may have higher demand during certain seasons or after new car model releases, allowing you to plan purchases accordingly.
Use historical data to prevent over-purchasing of slow-moving parts. By analyzing past sales performance, you can adjust inventory levels to maintain a balanced stock, ensuring profitability without tying up unnecessary capital in stagnant inventory.
Read for more: How to maximize your auto repair shop profit margin?
9- Implement a Return & Warranty Policy
Establish clear guidelines on how defective or returned parts should be handled to prevent financial losses. Without a structured return policy, businesses can accumulate faulty stock, wasting storage and costs.
Work closely with suppliers and manufacturers to streamline the return process, ensuring that damaged or defective parts are either replaced or refunded. This not only helps with financial recovery but also builds trust with customers and suppliers.
10- Train Staff on Inventory Best Practices
Educate employees on proper inventory handling, documentation, and tracking methods to reduce errors. Well-trained staff can improve inventory accuracy and efficiency, ensuring smooth operations.
Assign clear roles and responsibilities for inventory management to improve accountability. When each employee knows their specific duties, such as receiving stock, updating records, or auditing inventory, it reduces confusion and ensures consistency in management.
How Can Enerpize Help Track Auto Parts Inventory?
Enerpize is a comprehensive ERP system designed to streamline business operations with powerful automation, real-time tracking, and seamless integration across various departments. For auto repair and auto parts inventory management, Enerpize inventory management module simplifies auto parts management by offering real-time stock tracking, automated restocking alerts, and barcode-based categorization for quick retrieval.
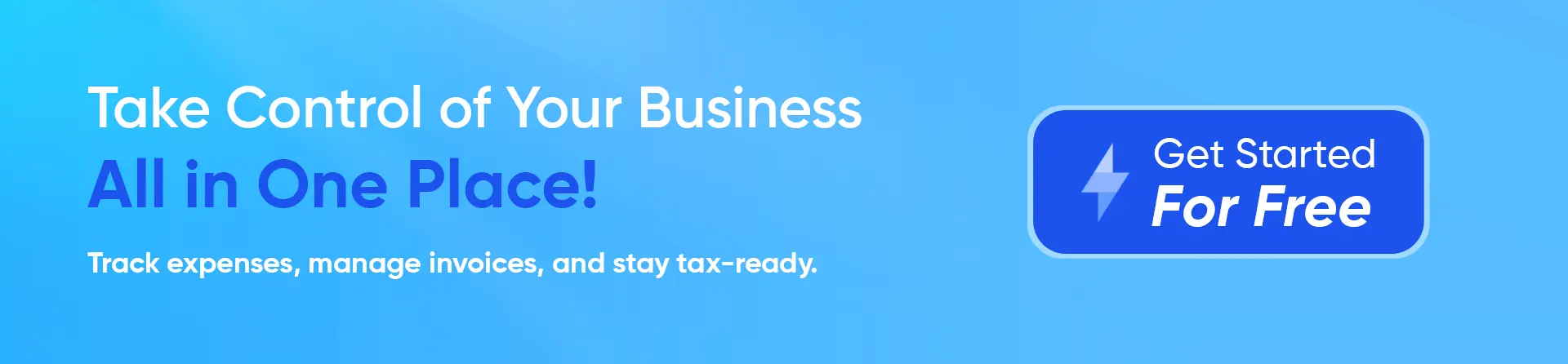
Enerpize's Auto Repair Shop Management Software ensures smooth integration with sales and invoicing, automatically updating stock when parts are used or sold. Businesses can efficiently manage supplier purchases, track returns, and monitor multi-location inventory to prevent shortages or overstocking. With detailed reports and analytics, repair shops can forecast demand, optimize purchasing, and control costs. Additionally, role-based access control enhances security, while cloud accessibility allows managers to monitor inventory from anywhere.
Managing auto parts inventory is easy with Enerpize.
Try our inventory module to manage your auto parts efficiency.