Create and send online quotations and invoices, track sales, monitor staff performance, and sell & sync all your products via our POS and more.
Author : Haya Assem
Reviewed By : Enerpize Team
What Are The Differences between Direct And Indirect Costs
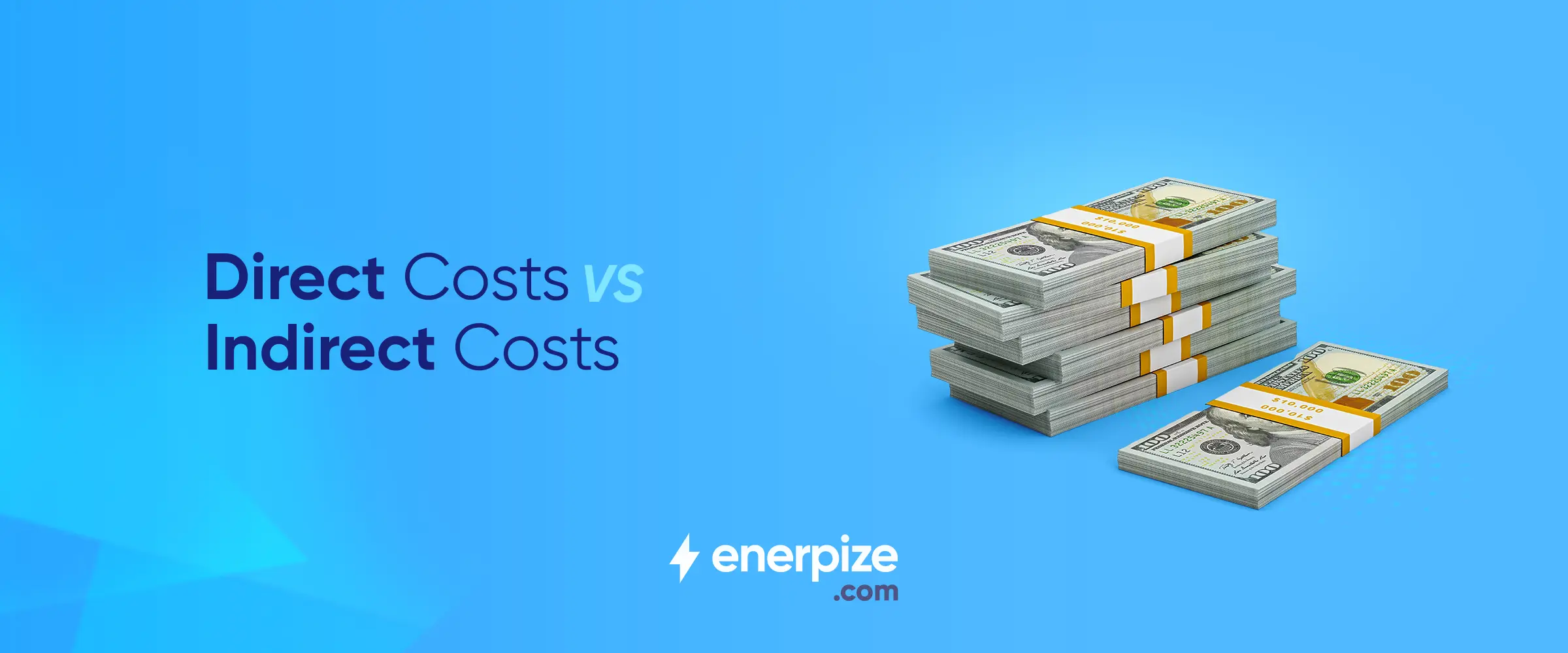
When managing a business, understanding where your money goes is essential. Every expense can impact your profitability, pricing, and financial planning. That’s why distinguishing between direct costs and indirect costs is critical. These two cost types serve different roles in your operations and accounting, and knowing how they differ helps you allocate resources effectively, set accurate prices, and improve your bottom line.
Key Takeaways
- Direct costs are expenses tied to specific products or projects, such as raw materials or wages for production workers, and they usually change with production levels.
- Indirect costs are general business expenses, like rent, utilities, and administrative salaries, which support operations but can't be linked to a single product or service.
- Knowing the difference between direct and indirect costs helps with accurate pricing, ensuring all expenses are covered without overcharging customers.
- Direct costs are straightforward to assign, while indirect costs must be allocated using methods like cost drivers or overhead rates.
- Tracking both cost types improves budgeting and financial forecasting, allowing businesses to plan better for future expenses and investments.
- Separating these costs supports detailed profitability analysis, showing how much profit each product or service actually generates.
What are Direct Costs?
Direct costs are expenses that can be clearly and directly traced to a specific product, service, project, or department. These costs are usually variable, meaning they change depending on the production or activity level. They are crucial for accurate budgeting, pricing, and profitability analysis.
Direct Costs Examples
Below are common examples of direct costs across various business activities:
- Raw Materials: The basic components used to manufacture a product. For example, wood for furniture or steel for machinery.
- Direct Labor: Wages paid to employees who are directly involved in the production process, such as assembly line workers or technicians.
- Production Supplies: Materials consumed during production that are specific to a product, like nails, paint, or adhesives.
- Packaging Costs: Custom or branded packaging used exclusively for a particular product or order.
- Freight and Delivery Charges: Shipping fees that are directly related to delivering a specific product to a customer.
- Sales Commissions: Commission paid to sales staff for selling a particular product or closing a specific deal.
- Job-Specific Equipment or Rentals: Costs for renting machinery or tools used exclusively for one project or product line.
What are Indirect Costs?
Indirect costs are expenses that are not directly tied to the production of a specific product or service, but are necessary for the overall operation of a business. These costs support the business’s general functioning rather than being directly attributable to a particular project or product.
Indirect Costs Examples
Indirect costs are typically spread across various products or departments. Here are common examples of them:
- Utilities: Costs for services like electricity, water, and heating that support the entire business but are not directly linked to one product.
- Rent: The lease payments for office spaces, warehouses, or facilities that benefit the entire organization.
- Administrative Salaries: Salaries paid to employees in roles such as management, HR, or accounting that support the business but don't directly contribute to production.
- Office Supplies: General supplies like paper, pens, and computers used throughout the business, not for a specific product.
- Depreciation: The gradual reduction in value of company assets such as office furniture, equipment, or vehicles used by the organization.
- Insurance: Premiums for general liability or property insurance that cover the entire company.
- Marketing and Advertising: Costs for promoting the business as a whole, including branding campaigns or general promotions not tied to a specific product.
- Maintenance and Repairs: Expenses related to maintaining or repairing equipment, machinery, or facilities used for general business operations.
Direct VS Indirect Costs
Understanding indirect vs direct costs is essential for accurate budgeting, pricing, and financial analysis. These two categories of expenses play distinct roles in cost accounting and affect how businesses evaluate profitability. Here are the key differences between the two categories:
Definition
- Direct costs can be directly traced to a specific product, service, or project.
- Indirect Costs support overall operations but cannot be tied to a specific output.
Traceability
- Direct Costs are easily traceable to a single cost object.
- Indirect Costs are not traceable to any one product or service.
Nature
- Direct Costs are usually variable—they change with production volume.
- Indirect Costs can be fixed, variable, or mixed, depending on the type of expense.
Examples
- Direct Costs include:
- Raw materials
- Direct labor
- Production supplies
- Indirect Costs include:
- Rent
- Utilities
- Administrative salaries
- Office supplies
Usage
- Direct Costs help determine unit cost and profit margin for each product or service.
- Indirect Costs help in understanding and controlling overhead costs and the business’s overall profitability.
Ease of Allocation
- Direct Costs are easily assigned to specific cost centers or products.
- Indirect Costs require allocation using predetermined rates or cost drivers.
Calculation Formula
Direct Costs are calculated using:
Direct Costs = Direct Materials + Direct Labor + Other Direct Expenses
Indirect Costs are calculated using:
Overhead Rate = Total Indirect Costs ÷ Total Allocation Base
Allocated Indirect Cost = Overhead Rate × Usage
Importance of Tracking Direct and Indirect Costs
Accurately tracking both direct and indirect costs is vital for maintaining financial clarity and making informed business decisions. By tracking direct and indirect costs, you can:
1- Improves Cost Control
Knowing exactly where money is being spent—whether on materials or overhead—helps businesses control unnecessary expenses and identify areas where cost-saving measures can be applied.
2- Supports Accurate Pricing
By separating direct from indirect costs, businesses can calculate the true cost of each product or service. This ensures prices are set high enough to cover all expenses and generate profit, without overcharging customers.
3- Enhances Budgeting and Forecasting
Tracking these costs allows for more accurate budgeting and financial forecasting. Direct costs help in projecting production expenses, while indirect costs give insight into overall operational needs.
4- Facilitates Profitability Analysis
Analyzing profits per product, project, or service becomes more meaningful when costs are categorized correctly. Direct costs show profit margins per unit, and indirect costs reveal how overhead impacts net profit.
5- Supports Better Decision-Making
When management understands the behavior and impact of both cost types, they can make smarter decisions about pricing, staffing, expansion, and investment.
6- Aids in Compliance and Reporting
Many accounting standards and tax regulations require businesses to separate direct and indirect costs. Proper tracking ensures compliance and accurate financial statements.
How can Enerpize help you in Tracking Costs
Enerpize is a cloud-based business management and accounting software designed to simplify operations for small and medium-sized enterprises. One of its core strengths is helping businesses accurately track and manage both direct and indirect costs. By offering a range of powerful features, Enerpize ensures that financial data is organized, transparent, and actionable.
Key Ways Enerpize Helps in Cost Tracking:
- Categorizes expenses into direct and indirect costs
- Allows cost allocation to specific products, projects, or departments
- Tracks overhead and distributes it using cost drivers
- Provides real-time financial and cost analysis reports
- Integrates inventory and payroll for automatic cost linking
- Offers dashboards and alerts to monitor spending patterns
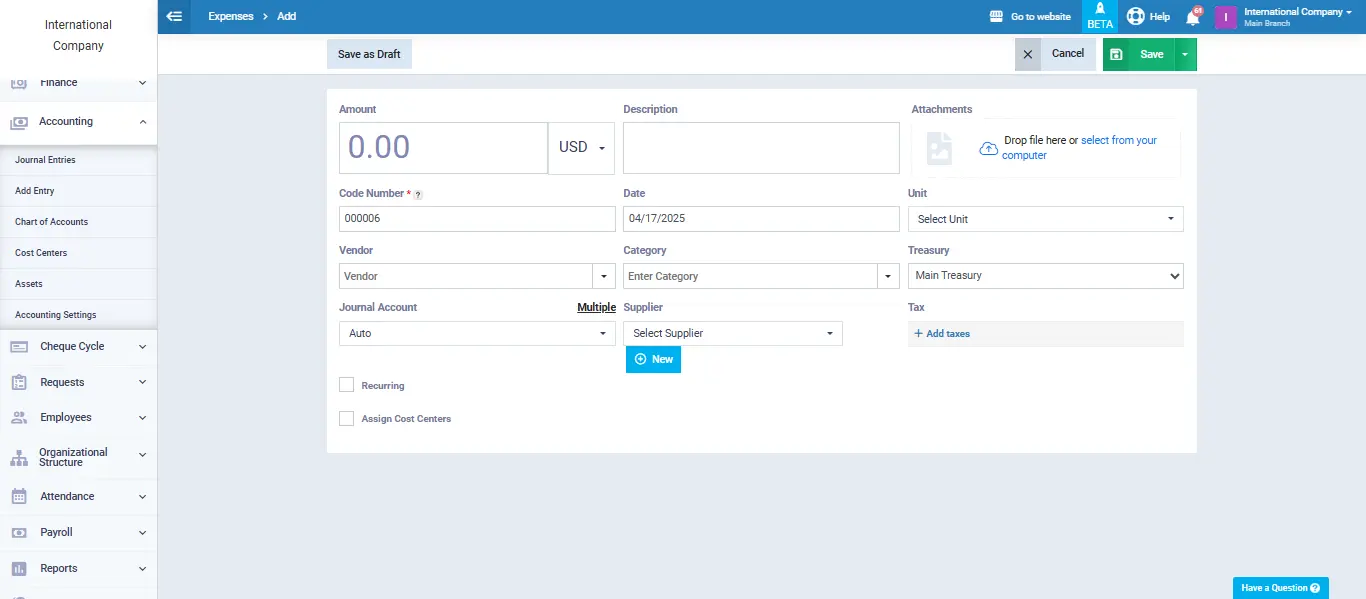
With these features, Enerpize gives businesses a clear and organized view of their cost structure. It reduces manual work, ensures accurate financial reporting, and supports better decision-making by helping users understand exactly where their money is going. Whether you're managing project costs or analyzing company-wide expenses, Enerpize keeps your cost tracking simple, accurate, and effective.
Managing your costs is easy with Enerpize.
Try our accounting module to manage your costs with ease.